What is the difference between medium wire cutting and fast wire cutting? How to distinguish them?
When we talk about medium wire cutting and high wire cutting, we are actually discussing two different processes in the field of electrical discharge wire cutting (EDM). Both technologies are common high-precision cutting methods in the manufacturing industry, and they have their own characteristics and applicable scenarios.
Zhikai servo wire cutting machine
Common points:
Let's understand the similarities between medium-speed wire cutting and high-speed wire cutting. Medium-speed wire cutting is a precision cutting technology that uses a thin wire as an electrode to cut the workpiece by electric spark discharge. The thin wire moves downward continuously during the cutting process, thereby achieving accurate cutting of the workpiece. Medium-speed wire cutting technology has the advantages of high precision, high finish and good processing stability, and is suitable for processing precision parts and complex special-shaped curved products. High-speed wire EDM wire cutting technology also cuts by the principle of electrode wire discharge.
Differences:
1. Misunderstanding
There is a misunderstanding here that the "fast" in the fast wire cutting machine refers to the fast cutting speed, which is what we call high cutting efficiency in the industry. It is mistakenly believed that the fast wire cutting machine has a faster cutting speed than the medium wire cutting machine. In fact, this is not the case. The "fast" and "medium" have no substantial meaning for the cutting efficiency of the machine tool.
2. Different programming, different finish
Fast wire is a type of EDM wire cutting, also called high-speed wire EDM wire cutting machine (WEDM-HS). It is the main machine type produced and used in my country. It is an original EDM wire cutting processing mode in my country and was used relatively early. The medium wire EDM machine was developed by Jiangsu Suzhou Wire Cutting Enterprise around 2003. It adds multiple cutting functions on the basis of the fast wire circuit. At that time, the medium wire was born, and the cutting finish is higher than the fast wire. The cutting surface is cut several times after cutting, and the finish is greatly improved. Different programming and different high-frequency power supplies lead to different finishes.
3. Machine differences and different precision
With the continuous influx of foreign wire cutting machines, such as Sodick wire cutting, Charmilles, etc., the accuracy and finish are far higher than the domestic medium-speed and high-speed wire cutting machines. The medium-speed wire cutting manufacturers are also constantly learning, optimizing and upgrading. Among them, the bed structure is the biggest change. From the initial F-type bed structure like the high-speed wire cutting, it has gradually developed into the current medium-speed wire cutting bed structure. This is a difference that can be seen with the naked eye. The casting materials used are also being improved, reducing the probability of machine deformation due to physical temperature changes. The guide rails and screws have also been improved, greatly improving the accuracy.
4. Differences in machine tool control systems
High-speed wire cutting uses an open-loop system, while medium-speed wire cutting machines have gradually transitioned from an open-loop system to a closed-loop system.
Wire cutting machine control systems have evolved from running on DOS computer systems to Windows XP, and now running on Windows 11 computer operating systems. Many new versions of drawing software are available. System functions have also developed from open loops to full closed-loop control systems for cool cutting systems.
Let's talk about the differences between open-loop, closed-loop and semi-closed-loop machine tool control systems.
An open-loop control system refers to a controller that controls the movement of the motor by sending command signals, but cannot provide real-time feedback on the actual movement of the motor. An open-loop control system is what we often call a stepper card, wire cutting stepper software. Medium-speed wire cutting machines are called steppers.
A closed-loop control system is one in which the controller uses sensors to provide real-time feedback on the position, speed and other information of the motor, and controls the motor based on the feedback information.
The semi-closed loop control system is a control method between open loop and closed loop, which controls the motor through partial feedback information. Compared with the open loop control system, the closed loop and semi-closed loop control system can more accurately control the position and speed of the motor and improve the machining accuracy and stability of the machine tool.
Closed loop and semi-closed loop are what we often call servo machines. The software is called servo wire-cut system, and wire-cut machine tools are called servo machines. Six-axis servo machine tools and five-axis CNC machine tools are both types of servo machines.
The control system is the heart of the machine tool, and the upgrade of the control system has brought about a significant improvement in the accuracy of the machine tool.
In medium-speed EDM wire cutting machines, the control circuit plays a vital role. The control circuit is responsible for controlling the movement and discharge process of the electrode to ensure the accuracy and stability of the cutting process. Being proficient in the design and debugging of the control circuit is one of the important skills of engineers who develop and manufacture medium-speed EDM machines. By optimizing the design of the control circuit, the machining accuracy and production efficiency of the machine tool can be improved to meet the machining requirements of different workpieces.
5. Stepper motor and AC servo motor
Fast wire cutting uses traditional stepper motor, while medium wire cutting machine tools are gradually replaced by AC servo motors.
The stepper motor is an open-loop control system that drives the motor to rotate by controlling the motor's pulse signal. The stepper motor has the advantages of simple structure, low cost, and easy control, and is suitable for some low-precision, low-speed, and low-load applications. However, the stepper motor has a step-out phenomenon during high-speed movement and high-precision positioning, which affects the processing quality. In contrast, the AC servo motor is a closed-loop control system with higher control accuracy and stability. It can monitor the position and speed of the motor in real time and control it according to the feedback signal, which is suitable for high-precision, high-speed, and high-load applications.
6. Screw wear
The wear of the lead screw will lead to poor processing accuracy, and the servo mid-wire system has a built-in pitch compensation correction function, which can effectively solve this problem. The lead screw will cause a decrease in processing accuracy due to friction and wear during long-term use. The servo mid-wire system uses the servo encoder to feedback the position and speed of the motor in real time, and can perform pitch compensation correction according to actual conditions to keep the processing accuracy at a high level. This automatic compensation function can reduce the impact of four-cylinder wear on processing accuracy and improve the long-term stability and accuracy of the machine tool.
(Note: There are many stepper signal to servo drive machine tools on the market. Although they are servo motors, they are actually open-loop systems like steppers. Users need to pay attention to identification when purchasing to avoid being deceived. You can judge according to the following points: 1. Walking speed (idle walking and jumping speed). At present, the walking speed of real servo systems is more than 20,000-50,000 steps, because they all use high-speed FPGA control, high walking accuracy and fast speed; if it is an open-loop system of stepper to servo, it is generally around 3,000 steps, and some are even only around 1,500 steps. 2. Whether it supports pitch compensation. The real servo system supports pitch compensation function, so that the mechanical wear can be compensated by software. The most intuitive way is to see whether the real-time walking data is fed back and displayed on the software. If not, it must be a stepper.)
High-speed wire generally does not use servo system, and stepper system does not have pitch compensation function.
7. Different levels of machine tool intelligence
The servo wire cutting machine control system has added many functions of the slow wire cutting machine. For example, the Cool Cut wire cutting servo system has built-in pitch compensation function, fast air cutting axis shifting, slow wire AR table, multi-user coordinate system, rotary axis processing, automatic centering advanced functions, which greatly improves the intelligence of the machine tool. These functions are unique to the servo wire cutting. In the field of spiral cutting, the Cool Cut system can realize rotary processing, and the six-axis linkage technology can realize the cutting of complex curved surfaces, which is suitable for precision machining fields such as automotive mold processing and aerospace mold processing.
The fast wire cutting system does not have these functions.
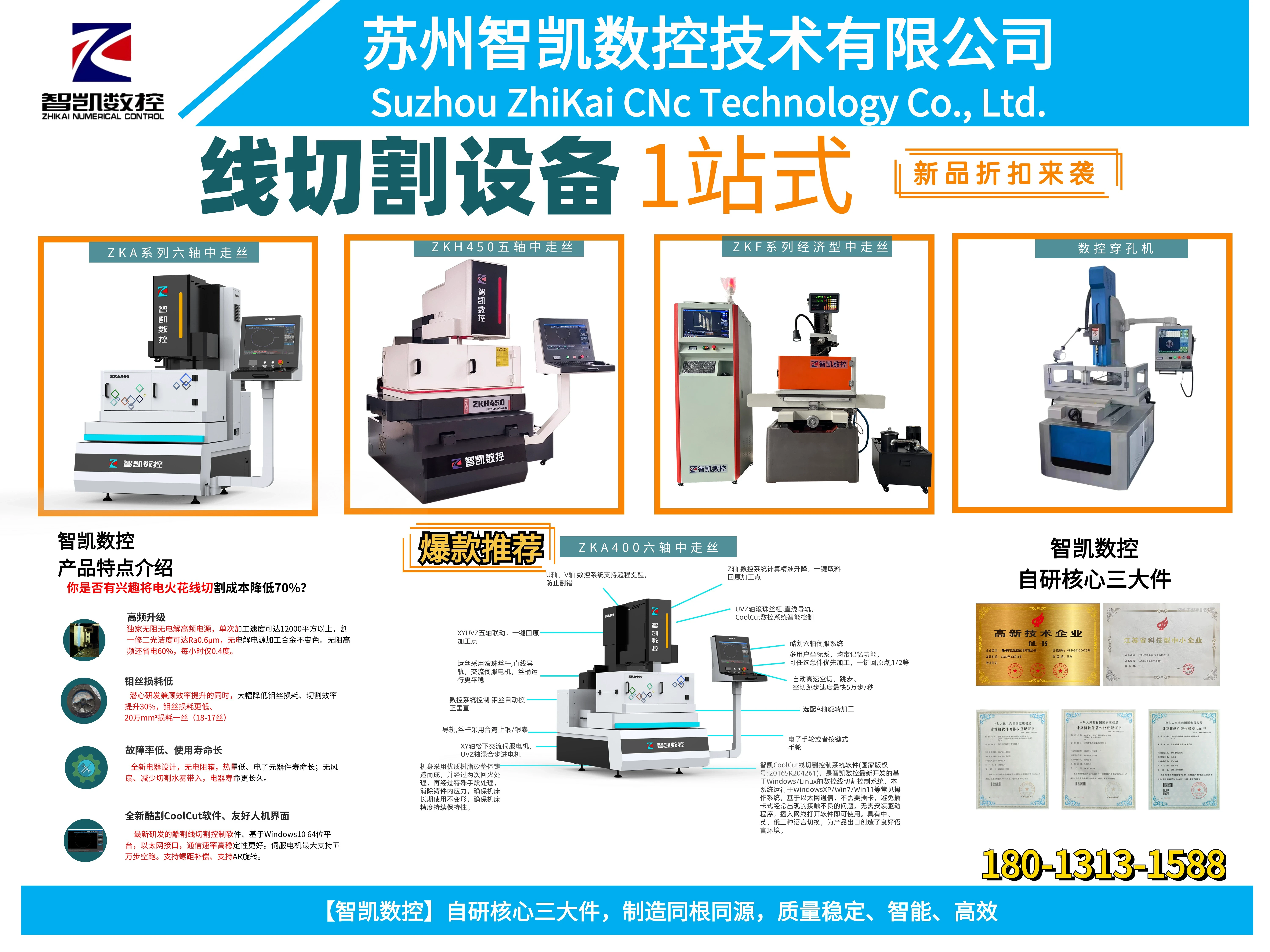
In comparison, medium wire cutting and fast wire cutting are two different processes in EDM wire cutting technology, which are suitable for precision cutting and fast cutting scenarios respectively. Medium wire cutting machine tools have rich experience and skills in mechanical manufacturing, control circuits and cool-cut wire cutting control systems, and can provide users with high-quality cutting solutions. Fast wire cutting is cheap and mainly solves rough primary processing such as mold blanking, and has different application scenarios. I hope that through the introduction of this article, readers will be able to better understand EDM wire cutting technology and choose suitable cutting processes and equipment for their own processing needs. Local friends in Suzhou can come to Zhikai CNC to experience it. The unique cutting pleasure of true servo medium wire cutting can also help you solve more processing problems. Consultation hotline: 180-1313-1588